Laminating Bottom and Sides
The second stage of the fiberglass work. A big milestone is reached with the hull lamination complete
After having laminated the bow and transom it was now time for the bottom and the sides. Again, I did this in two steps. I started off, by cutting the glass for both bottom and sides, as well as the reinforcements on the chines. I decided to cut the cloth along the length of the hull, rather than laying the glass perpendicular, like most builders have done. The thinking on this was, that it would create a larger overlap on the chines, strengthening them even more and also leaving me with less fairing that will have to be applied to make up for the uneven lamination schedule.
Before I started the lamination, the overlaps on the bow and transom were sanded down and the hull was cleaned. I usually degrease once more with acetone roughly 30 min before applying the resin. Like the previous laminations I first wetted out the wood and the biaxial glass bands and left them to soak for a while. The bands were pretty easy to apply, the twill and peel ply on the other hand were tough to do alone. I had prepared them carefully, rolled them up and marked where and how to lay them down but time never stops. By the time I had laid down the peel ply the resin I first applied was already tacky and I decided that for the sides I would need a resin guy.
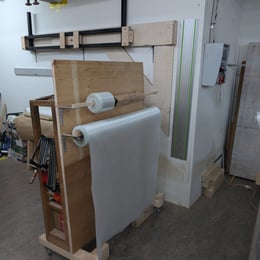
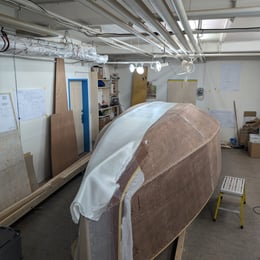
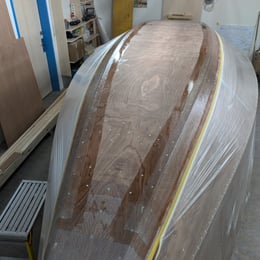
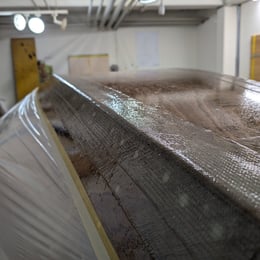
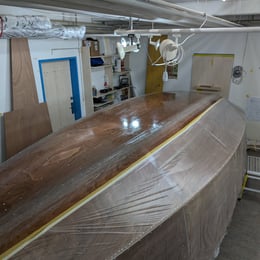
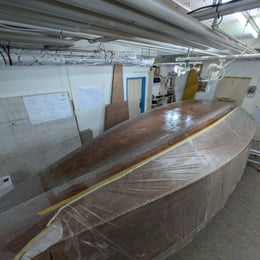
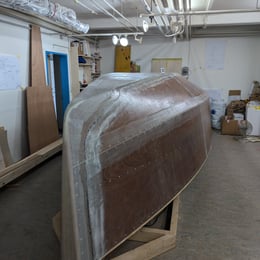
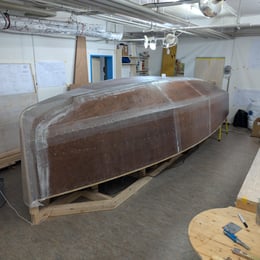
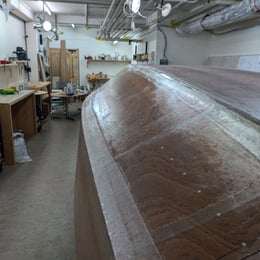
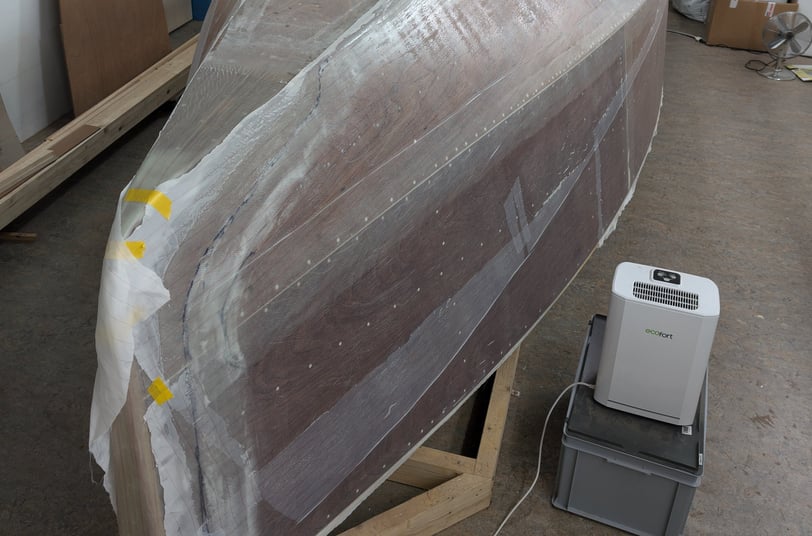
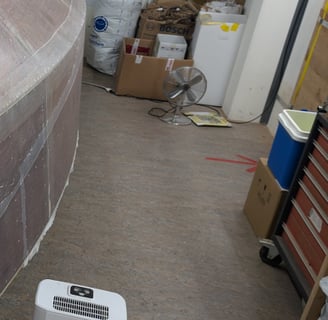


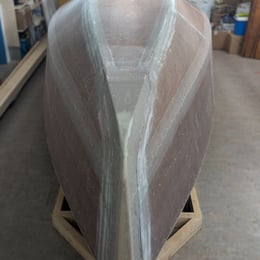
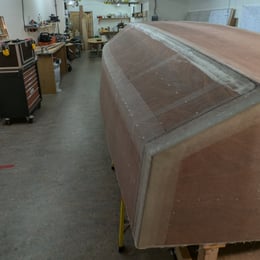
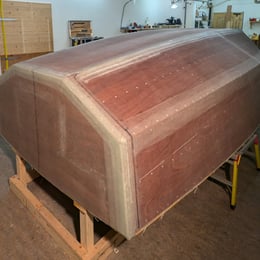
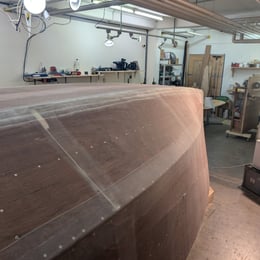
My brother joined me and the sides were laid up within about 6 hours. Having had help made the biggest difference since mixing the resin is so very time consuming. Also on the sides it would have been impossible to lay up the glass fabric alone. With four skilled hands and the Surface wetted out it was pretty simple to put the cloth down, as it stuck nicely to the hull. We had marked the overlap on the hull and worked top-down first port then starboard. The chine was cut on the hull. The fiberglass for the topsides was first laid to the correct overlap on the chine and then cut at deck level.
I removed the peel ply about two weeks after completing the lamination and sanded down the entire hull with a 60 grit sandpaper to remove any high spots, resin pockets and wrinkles and also to smooth out the overlaps.
Along the bow and the bottom chine we applied some thickened epoxy to not get any air bubbles trapped in the overlaps of the different layers of glass. I did do some sanding but wen laminating on to already cured glass, you cant be to careful. Any difference in level will try to lift of the overlapping layer of glass and cause air bubbles and delamination.
We also applied an additional layer of 600g/m^2 biaxial band over the joints of the hull plates within the planks
I am very happy with the result. Many thanks to my brother who was an excellent help both with mixing and laminating.