Laminating the Bow & Transom
Stage one and two of the lamination. Layup, resin, temperature, overlaps
The whole lamination process took me over one month as it was done in 4 stages. Bow and Transom on one weekend, bottom on the next weekend, and a couple of weeks later I did the sides with the help of my brother.
The transom was a pretty easy start and allowed me to get used to laminating again. it also allowed me to see and experience how viscose the resin was and how easily it would penetrate the glass fully.
Its the end of July and finally the summer had arrived, not quiet Ideal for me, but since my shop is in a basement, I could manage the temperatures. I used West System epoxy with the slow hardener. The temperatures were usually around 21°C in the morning and roughly 25° by late afternoon.
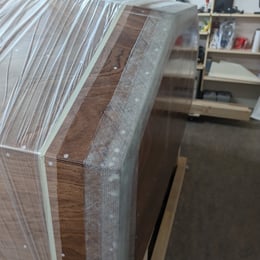
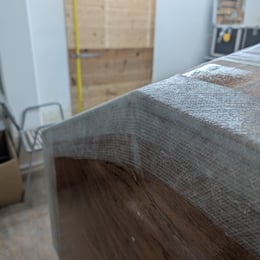
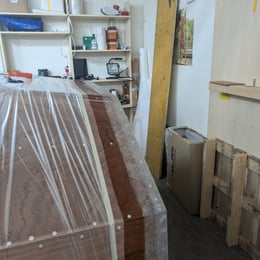
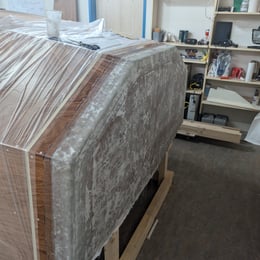
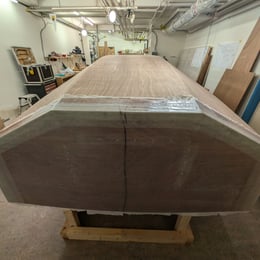
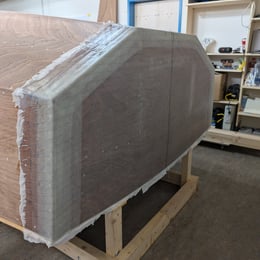
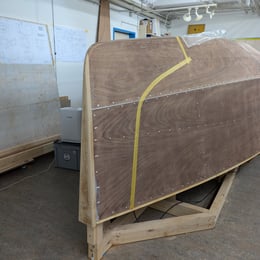
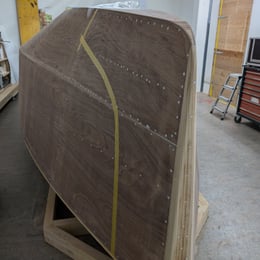
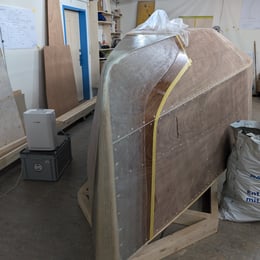
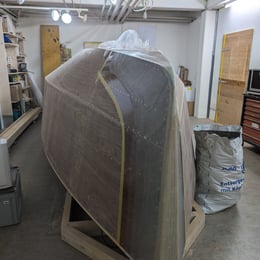
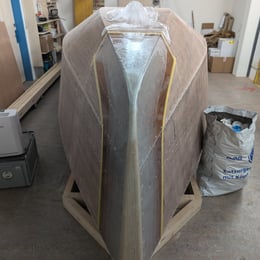
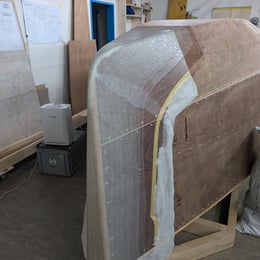
I laid up two, 600g/m^2 & 12.5cm wide biaxial glass bands all along the edge and overlapped them by 5cm. Then I added one more strip on the port and starboard side on the transom to help even out the inaccuracy that I had discovered. The glass bands were wetted out and left to saturate before applying them.
I then laid up two 280g/m^2 twill fabric also overlapping the previous layers by 5 cm. I marked and cut the wetted fabric on the hull. I didn't do any extra supports for the daggerboards because I doubled up the Ply on the inside and with the two layers of 280g twill i already over laminated by 360g.
The bow was a bit trickier to do because of the harsh curve of the bow-round. I used five layers of the 280g twill also overlapping by roughly 2.5 cm each. I was able to work the fabric around the bow by compacting into the bow-round (so no cutting). The five layers come out to 1400g/m^2 which is exactly what the laminate schedule calls for at the strongest parts (transom & bottom chine at 2x600g + 1x200g).
I finished off the lamination with a layer of peel-ply which was a lot harder to lay down than the actual glass fabric. I was pretty happy with the results. Almost no air bubbles trapped, and a nicely saturated glass laminate which even at 5 layers was pretty much see-through. During the hardening process the fabric pulled together a bit or at leas the peel ply did and left me with some minor wrinkles/pockets of resin on top. This is not a big problem but they will have to be addressed with a sander down the line.